
Use of Pressure Control in Chemical Manufacturing
Turning the raw material into a useful product is a complex task. It requires the manufacturer to perform a set of processes while maintaining the set quality standards. The quality of the product is the main key to building up a successful business. A manufacturer has to maintain the quality at each stage of the manufacturing process.
The word quality refers to the specifications that are necessary to fulfil and to manufacture the product as per the expectations. There are a set of inputs and process variables that need to be controlled for the precise happening of a process. To achieve this a pressure controller is frequently used in the manufacturing units. This controller keeps the pressure low and as well as the other process variables according to the need of the process.
Below we have listed a few reasons why controlling pressure is important in the chemical manufacturing sector:
Automation:
Today, the increasing costs have changed the working at industrial level. Most manufacturers have moved towards automated systems to perform all processes efficiently and fastly. Nowadays, the latest manufacturing units use complex machinery to produce the high-quality end products. This machinery requires performing all the tasks correctly. This accuracy is achieved with the help of a proportional flow control that lets the machines to operate on the required pressure.
Safety:
In the chemical and petrochemical sector, the manufacturer has to carry out hazardous processes for manufacturing the end product. This kind of manufacturing needs great care and requires the operator to manage and control the process variables accurately. A small change in the pressure of the gases can be very dangerous and can become the reason for an unpleasant incident like an explosion. This is the main reason for using a high pressure controller in the manufacturing sector. It ensures the safety of the workers and the system by keeping pressure and other process variables under control.
Saves Energy:
Large manufacturing units consume a huge amount of energy which reluctantly enhances the production cost for the manufacturer. That’s why the manufacturers always keep looking for ways to cut down the cost and keep trying to make their manufacturing units more energy efficient. In this regard, a proportional valve controller serves a key role. In manufacturing plants, various fluid and air-powered systems and equipment are used to perform different tasks. They need a precise amount of pressure to operate accurately. When the system will use an equal amount of pressure and energy to perform all the tasks then the excess pressure and energy will go to waste. But with the help of a pressure control, the operator can provide the correct pressure to each system and equipment. This way, it lowers the consumption of energy.
Reducing the Cost:
An electronic pressure control helps the systems and machinery to use precise pressure and reduce the waste of excess pressure. Whenever a system uns on the optimum pressure as per the need then the waste is low and there are fewer chances to produce the defective products. Resultantly, production and repair cost goes down.
Final Words:
As we know that pressure and other process variables like temperature etc should be managed appropriately for a chemical manufacturing process to happen precisely. Any changes in these optimal parameters impact the end product. But pressure controllers let the manufacturers keep all the process variables under control. That's why these devices have great importance in the chemical manufacturing sector.
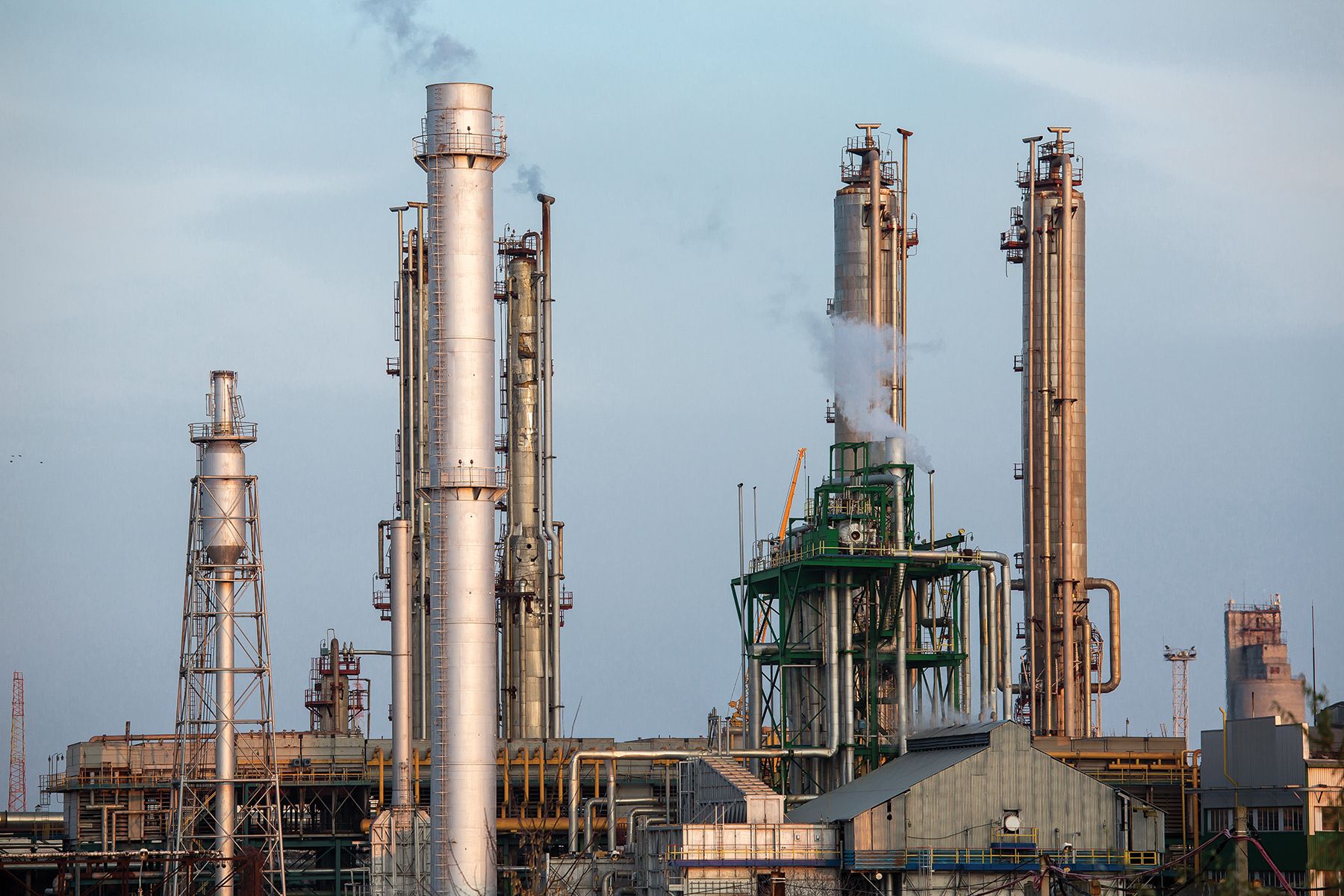
Chemical Manufacturing