
The Ultimate Guide to Flux Core Welders
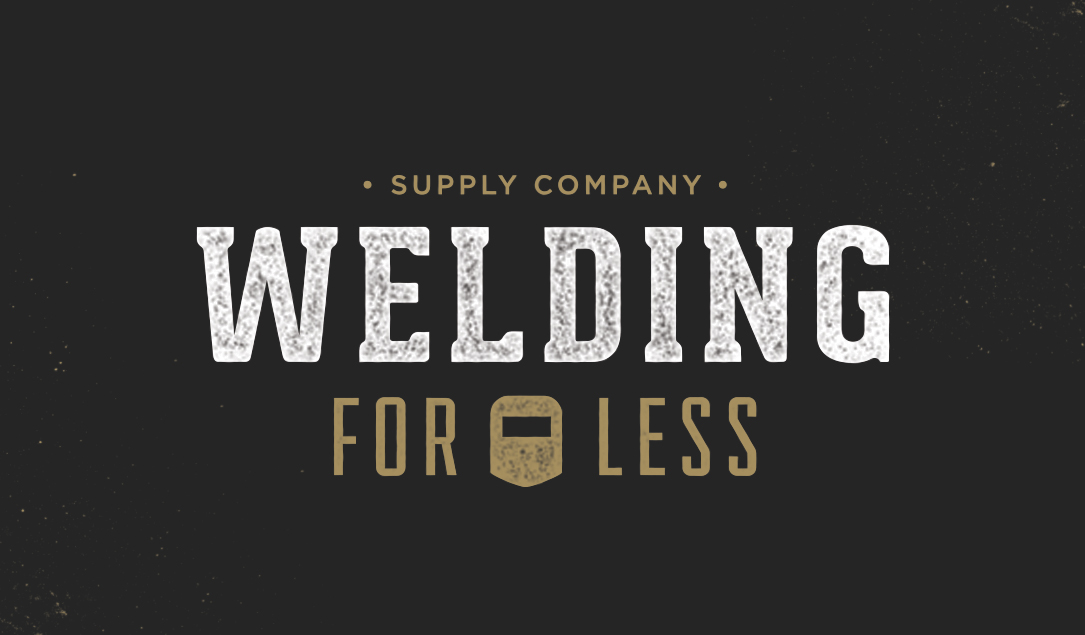
Flux core welding has become increasingly popular in recent years due to its versatility, portability, and ease of use. Whether you're a seasoned welder or just starting, understanding flux core welders and their applications is essential. In this comprehensive guide, we'll cover everything you need to know about flux core welding wire welders, from how they work to tips for getting the best results.
1. What is Flux Core Welding?
Flux-core welding, also known as flux-cored arc welding (FCAW), is a semi-automatic welding process that uses a continuous wire electrode with a flux-filled core. Unlike traditional MIG welding, which relies on a shielding gas to protect the weld pool from atmospheric contamination, flux core welding generates its shielding gas from the flux within the electrode. This makes flux core welding ideal for outdoor and windy conditions where shielding gas can be blown away.
Flux core welding can be performed with both gas-shielded and self-shielded electrodes, offering flexibility in various welding applications. Gas-shielded flux core welding provides cleaner welds with less spatter, while self-shielded flux core welding is more portable and doesn't require an external shielding gas source. Understanding the differences between these two types of flux core welding is crucial for selecting the proper process for your specific needs.
2. Types of Flux Core Welders
Flux core welders come in various types and configurations to suit different welding tasks and skill levels. The most common types of flux core welders include:
Flux Core MIG Welders: These machines are capable of both MIG and flux core welding, offering versatility for a wide range of applications.
Dedicated Flux Core Welders: These machines are designed explicitly for flux core welding, providing optimized performance and efficiency.
Portable Flux Core Welders: Compact and lightweight, these welders are ideal for on-the-go welding tasks and outdoor projects.
When choosing a flux core welder, consider factors such as power output, duty cycle, wire feed speed control, and compatibility with different wire sizes. Investing in a quality flux core welder that meets your specific requirements will ensure reliable performance and consistent weld quality.
3. Advantages of Flux Core Welding
Flux core welding offers several advantages over other welding processes, making it a popular choice for both amateur hobbyists and professional welders. Some key advantages of flux core welding include:
Increased Penetration: The flux core wire produces a deeper weld penetration compared to solid wire MIG welding, making it suitable for welding thick materials.
All-Position Welding: Flux core welding can be performed in all positions, including overhead and vertical, allowing for greater flexibility and accessibility in tight spaces.
Improved Outdoor Performance: The self-shielding capability of flux core wire makes it less susceptible to atmospheric conditions, making it ideal for outdoor welding tasks where wind and drafts can interfere with shielding gas coverage.
Cost-Effectiveness: Flux core welding typically requires fewer equipment and consumables compared to traditional MIG welding, resulting in cost savings for welders on a budget.
Understanding the advantages of flux core welding can help you leverage its capabilities effectively for various welding projects. Whether you're working on structural steel fabrication, automotive repair, or shipbuilding, flux core welding offers significant benefits in terms of efficiency, versatility, and cost-effectiveness.
4. Applications of Flux Core Welding
Flux core welding finds applications in a wide range of industries and projects thanks to its versatility and effectiveness. Some typical applications of flux core welding include:
Structural Steel Fabrication: Flux core welding is widely used in the construction industry for fabricating structural steel components such as beams, columns, and trusses.
Shipbuilding and Marine Repairs: Flux core welding is well-suited for welding thick steel plates and ship structures, making it a preferred choice for marine applications.
Automotive Repair and Maintenance: Flux core welding is commonly used in automotive workshops for repairing body panels, exhaust systems, and chassis components.
Pipe Welding: Flux core welding is ideal for welding pipes and pipelines in industries such as oil and gas, water treatment, and plumbing.
Outdoor Construction Projects: The self-shielding capability of flux core welding makes it ideal for outdoor construction projects where shielding gas can be impractical or unavailable.
By understanding the diverse applications of flux core welding, you can harness its capabilities to tackle various welding projects with confidence and efficiency. Whether you're working in a fabrication shop, on a construction site, or in your garage, flux core welding offers the versatility and performance you need to achieve high-quality welds.
5. Choosing the Right Flux Core Welding Wire
Selecting the suitable flux core mig welding wire is crucial for achieving optimal weld quality and performance. Flux core welding wires come in different types, sizes, and compositions, each suited to specific welding applications and materials. Some key factors to consider when choosing flux core welding wire include:
Wire Diameter: Flux core welding wires are available in various diameters, typically ranging from 0.030 to 0.045 inches. The wire diameter you choose should match the thickness of the base metal you're welding.
Wire Composition: Flux core welding wires are available in different compositions, including mild steel, stainless steel, and flux-cored aluminum. Selecting the appropriate wire composition is essential for achieving the desired mechanical properties and corrosion resistance in the welded joint.
Flux Composition: The flux composition of flux core welding wire plays a significant role in the welding process, affecting weld penetration, bead shape, and slag formation. Different flux formulations are optimized for specific welding applications, such as deep penetration welding, high-speed welding, or welding in windy conditions.
By carefully selecting the suitable flux core welding wire for your specific welding task, you can ensure optimal weld quality, productivity, and performance. Consult with welding suppliers or manufacturers to determine the best wire type and composition for your application requirements.
6. Setting Up Your Flux Core Welder
Proper setup and adjustment of your flux core welder are essential for achieving consistent weld quality and performance. Follow these steps to set up your flux core welder correctly:
Select the appropriate wire size and type for your welding application, ensuring compatibility with your welder's wire feed system.
Install the flux core welding wire spool onto the wire feed mechanism, ensuring proper alignment and tension.
Adjust the wire feed speed and voltage settings on your welder according to the manufacturer's recommendations and welding parameters for the specific wire diameter and material thickness.
Set up the welding machine for the desired welding process (gas-shielded or self-shielded flux core welding), adjusting the polarity and gas flow rate as necessary.
Ensure that all welding cables and connections are secure and free of damage or corrosion, providing a reliable electrical circuit for the welding operation.
Perform a test weld on scrap material to verify the weld settings and make any necessary adjustments to achieve the desired weld bead appearance and penetration.
Proper setup and calibration of your flux core welder are critical for achieving consistent and high-quality welds. Take the time to familiarize yourself with your welder's operation manual and recommended welding parameters to ensure optimal performance and safety.
7. Flux Core Welding Techniques
Flux core welding requires specific techniques to achieve optimal weld quality and performance. Here are some essential flux core welding techniques to master:
Travel Speed: Maintain a consistent travel speed along the weld joint to ensure uniform heat distribution and weld bead formation. Too fast of a travel speed can result in incomplete fusion, while too slow of a travel speed can lead to excessive heat input and distortion.
Arc Length: Maintain a consistent arc length between the welding electrode and the workpiece to ensure stable arc conditions and proper weld penetration. Keep the arc length short but stable to prevent spatter and ensure good arc stability.
Electrode Angle: Hold the welding electrode at the appropriate angle relative to the workpiece, typically between 5 to 15 degrees in the direction of travel. This angle helps control weld penetration and bead shape while minimizing spatter and slag entrapment.
Weaving Technique: Employ a weaving motion (back and forth or side to side) along the weld joint to ensure uniform weld bead width and fusion. Be mindful of the weaving amplitude and frequency to prevent excessive buildup and maintain proper sidewall fusion.
Post-Weld Cleaning: After completing the weld, remove any slag or spatter from the weld bead using a wire brush or chipping hammer. This ensures a clean weld surface and facilitates visual inspection and subsequent welding passes if necessary.
Mastering these flux core welding techniques takes practice and experience, but with dedication and perseverance, you can achieve consistent and high-quality welds in various welding positions and applications.
8. Common Flux Core Welding Defects and How to Avoid Them
Despite your best efforts, flux core welding can sometimes result in defects that compromise weld quality and performance. Here are some common flux core welding defects and tips for preventing them:
Porosity: Porosity occurs when gas pockets are trapped within the weld metal, compromising its strength and integrity. To prevent porosity, ensure proper gas shielding (if using gas-shielded flux core wire) and maintain a clean welding environment free of contaminants such as oil, rust, or moisture.
Slag Inclusions: Slag inclusions occur when welding slag becomes trapped within the weld metal, creating discontinuities and weakening the weld joint. To avoid slag inclusions, ensure proper flux coverage and remove slag between welding passes using a wire brush or chipping hammer.
Lack of Fusion: Lack of fusion occurs when the weld metal fails to fuse with the base metal or previous weld pass, resulting in incomplete penetration and weak weld joints. To prevent a lack of fusion, ensure proper joint preparation, welding technique, and sufficient heat input to achieve proper fusion.
By understanding the causes of common flux core welding defects and implementing preventive measures, you can minimize weld rework and ensure consistent weld quality and performance.
9. Safety Considerations for Flux Core Welding
Safety should always be a top priority when performing any welding operation, including flux core welding. Here are some essential safety considerations to keep in mind:
Personal Protective Equipment (PPE): Wear appropriate PPE, including a welding helmet with a properly shaded lens, flame-resistant clothing, welding gloves, safety glasses, and closed-toe leather boots, to protect yourself from sparks, UV radiation, and heat.
Ventilation: Ensure adequate ventilation in the welding area to remove welding fumes and gases, preventing exposure to hazardous airborne contaminants. Use local exhaust ventilation systems or work in well-ventilated areas whenever possible.
Fire Prevention: Keep a fire extinguisher nearby and familiarize yourself with its proper use in case of welding-related fires. Remove combustible materials from the welding area and take precautions to prevent sparks from igniting nearby flammable substances.
Electrical Safety: Inspect welding cables and connections for damage or wear and ensure proper grounding of the welding machine to prevent electric shock hazards. Avoid contact with live electrical parts and use insulated tools and equipment when working near energized circuits.
By prioritizing safety and adhering to proper welding practices, you can minimize the risk of accidents and injuries associated with flux core welding, ensuring a safe and productive work environment.
10. Maintenance and Care of Flux Core Welding Equipment
Proper maintenance and care of your flux core welding equipment are essential for prolonging its lifespan and ensuring reliable performance. Here are some maintenance tips to keep your flux core welding equipment in top condition:
Regular Inspection: Perform regular visual inspections of your flux core welder, welding cables, torch, and other components to check for signs of damage, wear, or corrosion. Replace any worn or damaged parts promptly to prevent equipment failure or safety hazards.
Cleanliness: Keep your flux core welder and welding accessories clean and free of dirt, dust, and debris that can interfere with their operation. Use compressed air or a soft brush to remove buildup from cooling fans, wire feed mechanisms, and electrical connections.
Lubrication: Lubricate moving parts and components of your flux core welder as recommended by the manufacturer to ensure smooth operation and prevent premature wear. Use high-quality lubricants suitable for welding equipment and follow proper application procedures.
Calibration: Periodically calibrate your flux core welder's settings and parameters according to the manufacturer's recommendations to maintain accurate performance and weld quality. Use calibration tools and test equipment to verify voltage, wire feed speed, and other critical parameters.
By following these maintenance practices and caring for your flux core welding equipment, you can prolong its lifespan, minimize downtime, and ensure consistent and reliable performance for all your welding projects.
Conclusion
Flux core welding offers numerous benefits, including increased penetration, all-position welding capability, and improved outdoor performance, making it a popular choice for welders in various industries and applications. By understanding the fundamentals of flux core welding, selecting the right equipment and consumables, mastering welding techniques, and prioritizing safety and maintenance, you can achieve consistent and high-quality welds for all your welding projects. Whether you're a beginner or an experienced welder, the knowledge and skills gained from this ultimate guide to flux core welders will empower you to tackle welding tasks with confidence and efficiency.