
How to Designed Canned Motor Pump?
A canned motor pump is designed to handle fluids hermetically. A shaft seal-free canned motor pump has a pressure-proof motor casing and magnetic couplings to ensure that fluids do not escape. Similarly, a shaft-sealed canned motor pump does not allow any leakage or ingress of air.
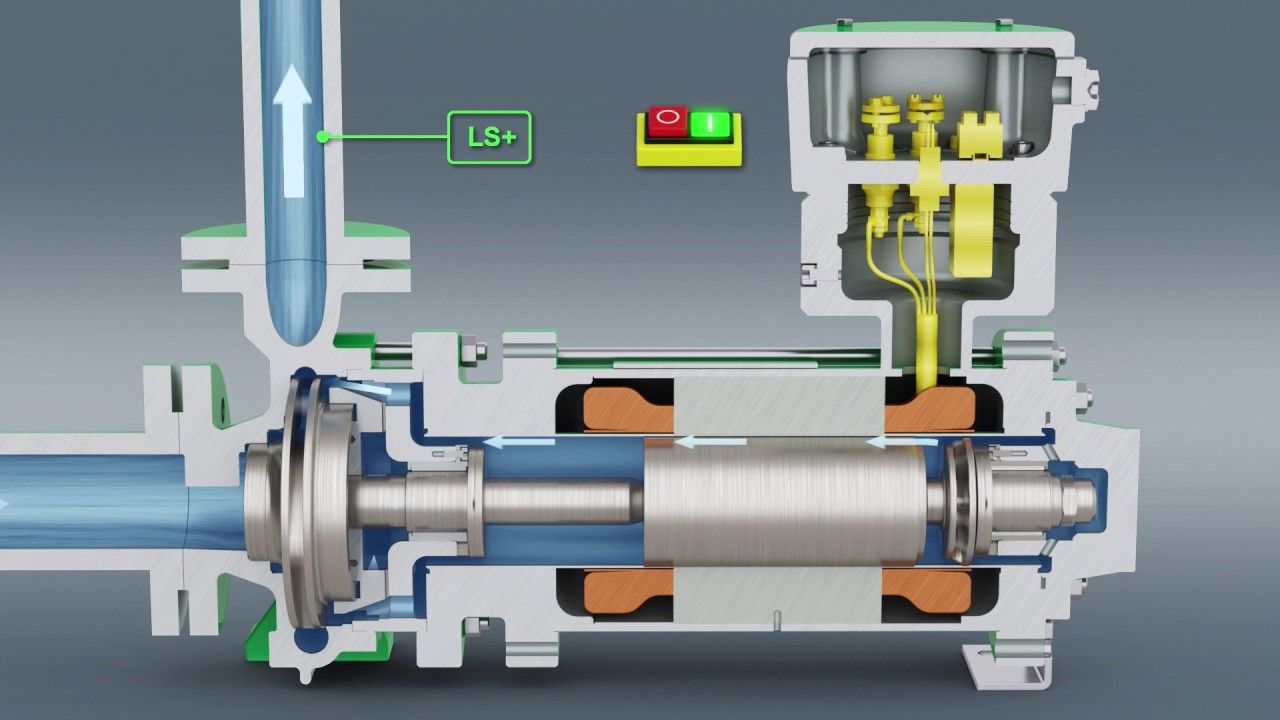
F.N Engineering
F.N Engineering is one of the leading European manufacturers of canned motor pumps. With more than 180,000 pumps supplied to customers worldwide, the company is a key player in the industry. In addition to its headquarters in Germany, the company has subsidiaries in China and the USA. Their goal is to provide superior products and reliable customer service throughout the entire plant lifecycle.
The F.N Engineering brand is an expert in sealing solutions for industrial applications. They manufacture a variety of standard and customized designs to meet customer needs. Their range includes pumps for fluid temperatures ranging from -160 deg C to +450 degC and system pressures up to 120 MPa. HERMETIC pumps are safe, durable, and smooth to operate.
Rutschi
A Rutschi canned motor pump features a feed and discharge line. The feeding line connects pump chamber 58 to the canned motor section 52. The discharging line connects to the pump section 50's lower pressure side through the balancing hole 96. The feeding line also provides lubrication to the pump's front bearing 70.
The canned motor pump is an efficient choice for high-temperature liquids. Because the pump absorbs the entire motor's heat, it is a cost-effective liquid-feeding system. This reduces the thermal load of the heating source and eliminates energy losses. Moreover, the pump uses a heat-absorbing fluid that is recycled in the pump section.
Another feature of the Rutschi canned motor pump is its jacket. It is mounted on the outer wall of the motor section. It is made of special silicone filled with fluoro-mica. This material is cured after being impregnated. This type of pump has many advantages, including the ability to be easily maintained.
Centrifugal pumps
The main difference between centrifugal pumps and canned motor pumps is the type of motor used. The former uses a squirrel cage rotor, while the latter uses a lamination pack and rotor bars connected to short-circuit rings. Both types of pumps use centrifugal force to move fluids, and they are self-damping. However, canned motor pumps are generally less efficient than their air-cooled counterparts.
Canned motor pumps can be configured to mimic or approach the envelope of a standard centrifugal pump. In addition to avoiding the need for regular emissions monitoring, they can be configured to run in extreme temperatures and with aggressive fluids.
Shaft seal-free
Shaft seal-free canned motor pumps are an environmentally friendly alternative to conventional centrifugal pumps. These pumps are preferred in the petrochemical and chemical industries. Many models are available in stock and can be shipped to customers within a few days. In addition to being a greener option, these pumps also have fewer mechanical seals, which can lead to increased reliability and lower maintenance costs.
The UCWC model features an innovative back-pull-out design that allows you to disassemble and inspect the rotary parts without removing the casing. This feature reduces the time and risk of nonconformity during installation. It is also a cost-effective solution and can be manufactured for as little as $40.
Compact
Compact canned motor pumps feature a compact design and are designed to meet a variety of application requirements. Some models are designed for liquids and others for gas applications. These motor pumps can handle a wide range of fluids and temperatures and include options for high pressure and high melting points. They also have no lubrication oil, which reduces maintenance and contamination concerns. The compact motor shaft also minimizes operation noise.
The operating circuit of a compact canned motor pump is designed to withstand high temperatures. Its secondary cooling and lubricating circuit have a low-temperature capacity of about 60 to 80 degrees Celsius. Its winding is constructed with durable insulation class H. The centrally-positioned fins improve heat dissipation by natural convection.