
Choosing Right Cathodic Protection Contractors for Your Project
Cathodic protection is a widely used method to ensure corrosion protection of underground or submerged assets such as pipelines, the bottoms of storage tanks in industrial plants or metal reinforcements in concrete buildings or bridges. Originally developed in the first half of the 19th century to protect warships' metal hulls, cathodic protection is now applied to many large structures. Water heaters or boilers are often protected using this technology too.
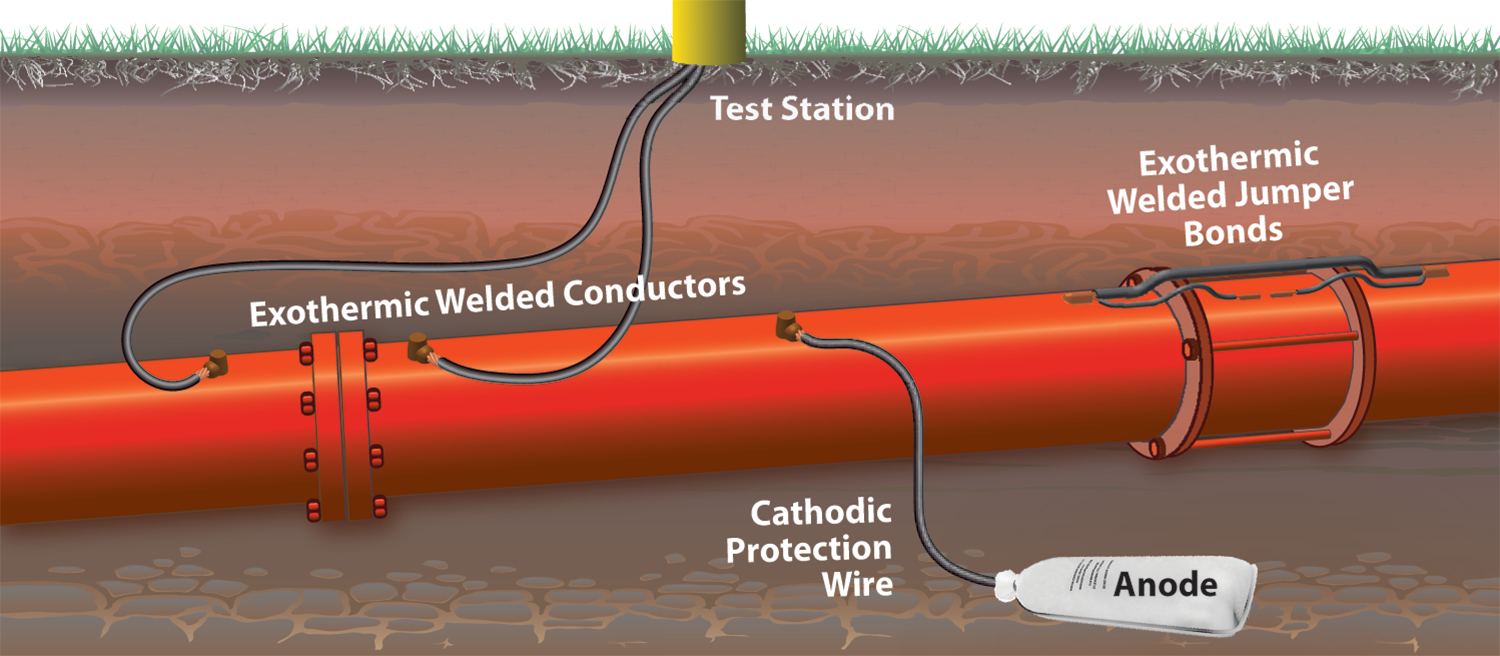
Pipeline Corrosion Testing
Cathodic Protection Contractors use a variety of methods to assess pipeline corrosion. The tests can include soil resistivity, stray current and component electrical isolation measurements of buried metal piping and tank systems.
Some Cathodic Protection Contractors may also use the X-ray or Radiography method to detect changes in pipe wall thickness caused by corrosion. However, this method is only effective for small areas and it can pose a radiation hazard to the radiography personnel performing the inspection.
Corrosion monitoring is an important tool for controlling pipeline corrosion. The accuracy of a corrosion monitoring program relies on accurate data input. This data includes pipeline description (diameter of pipe and pipe thickness), product type, maximum operation pressure, operation temperature, soil specification, last inspection date, condition of coating and density of population, pipeline age, pressure in the pipeline and corrosion specification depth, width and length.
Testing Stations
Cathodic Protection Contractors provide testing stations, line markers, rectifiers and more to oil, gas and water pipeline operators. These services often include excavation, shoring and electrical work depending on the location, client and regulatory body overseeing the project.
Test stations are an essential component of cathodic protection systems. They allow technicians to terminate cables from buried structures and take electrical measurements or readings of that structure to determine if the system is working properly.
The equipment needed to do this includes a voltmeter/ammeter (multimeter), reference electrode, wires, clips and test probes. The test stations are typically affixed to the ground or a concrete structure above it.
The test station will also include other testing components such as current measurement shunts, on/off switches and bond jumpers. While this may seem like a lot of equipment, it is very simple to install and maintain. It is important that these test stations are maintained in good working order and free from corrosion and contamination to ensure a proper operation.
Anode Installation
Cathodic Protection Contractors can install a number of different types of anodes to prevent corrosion. This includes galvanic, impressed current, and sacrificial anodes.
The type of anode that is most appropriate for your pipeline will depend on its environment and current demands. For example, a pipeline with low current demands will be more cost effective to protect using galvanic anodes than one that has high current demands.
Whether you’re looking to keep your water or oil pipelines safe, Cathodic Protection Contractors have the expertise and experience necessary to properly install anodes. They are equipped with NACE certified construction managers, equipment operators, and corrosion technicians to ensure your pipeline is protected.
Test Station Maintenance
Cathodic protection contractors testing is done for oil, gas and water pipelines, above ground storage tanks, power plants, energy facilities, deep wells and other infrastructure assets. NACE certified experts analyze the test results and make recommendations for system maintenance.
The test station usually includes a monitoring/access box, one or more reference electrodes and associated wiring. These are installed at regular intervals along the pipeline to provide the pipeline operator with valuable operational details.
A test station is essential for the proper functioning of an impressed current or galvanic sacrificial anode system. The test station may also need a jumper wire between each pipe couple in order to assure electrical continuity between sections of the piping system that are being protected.
Cathodic protection systems can be difficult to test without the proper training and equipment. In addition, they require accurate records and periodic inspections to insure that they are operating correctly.