
3d Printing and Vacuum Casting
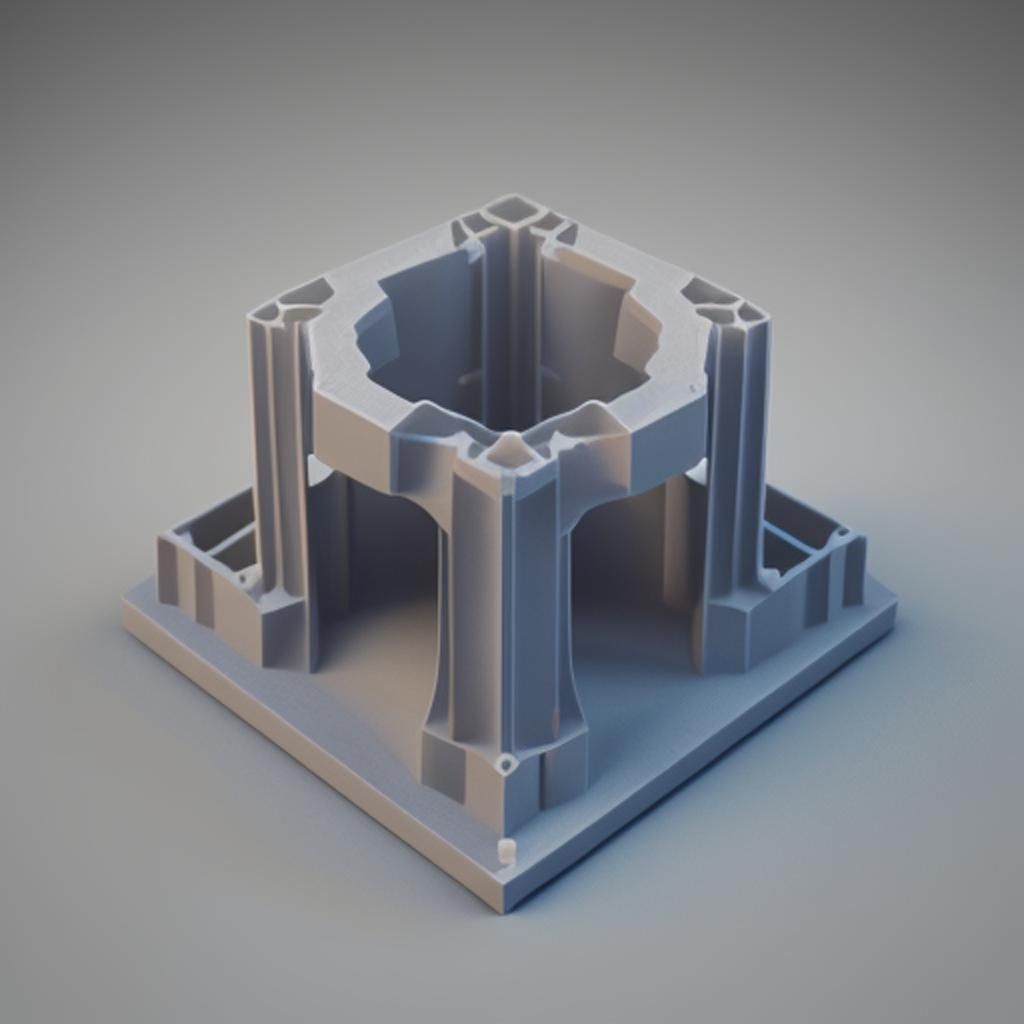
Rapid prototyping technologies like 3D printing and vacuum casting are transforming the way products are designed, prototyped, and manufactured. These innovative processes enable faster design iteration, lower costs, and more customization compared to traditional manufacturing methods. This guide provides an in-depth look at how 3D printing and vacuum casting work, their respective benefits and limitations, and how they are best utilized.
How Does 3D Printing Work?
Also known as additive manufacturing, 3D printing constructs physical objects layer-by-layer from digital 3D model data. Here are the basic steps:
A digital 3D model is designed using CAD software and converted to an STL file readable by 3D printers.
The STL file is processed through slicing software which divides the model into thin layers and generates toolpaths for the print head.
The 3D printer deposits or solidifies material, layer by layer, as guided by the toolpaths. Thermoplastics like ABS and PLA are commonly used.
Supported structures prevent overhanging layers from collapsing during printing. These are later removed.
After completion, any additional finishing work like sanding or painting can be done to smooth surfaces.
3D printing technology provides unmatched geometric freedom compared to subtractive methods like CNC machining. Complex shapes with internal voids or lattices are possible. When discussing the wonders of additive manufacturing, you can find valuable insights here.
Different Types of 3D Printing Processes
There are several distinct 3D printing technologies currently in use:
Fused Deposition Modeling (FDM) - One of the most common methods, FDM works by heating thermoplastic filament and extruding it through a nozzle to deposit layers. ABS and PLA filaments are low-cost.
Stereolithography (SLA) - A UV laser solidifies photopolymer resin layer-by-layer in a vat. SLA produces smooth, durable parts with fine detail resolution.
Selective Laser Sintering (SLS) - A high-power laser fuses and sinters powder material like nylon, glass, or metal. SLS allows for complex geometries.
Multi Jet Fusion (MJF) - Inkjet printheads deposit fusing and detailing agents onto nylon powder beds which are then sintered with an infrared lamp.
Direct Metal Laser Sintering (DMLS) - A laser melts and fuses metallic powder into solid metal shapes. DMLS is used to 3D print end-use metal components.
Each process has tradeoffs in terms of part properties, materials, accuracy, speed, and cost that make them suitable for different applications. To explore the possibilities of precision molding, visit this source
Benefits and Limitations of 3D Printing
Understanding the advantages and disadvantages of 3D printing is important:
Benefits
Design freedom for complex geometries
Fast turnaround for prototyping
Customization and low volume production
Reduced waste compared to subtractive methods
Consolidation of assembly through printed articulations
Limitations
Lower accuracy/higher tolerances than machining
Limited choice of materials and mechanical properties
Typically slower than mass production techniques
Smaller build volumes limit part size
Horizontal layer lines cause anisotropic strength
While 3D printing has restrictions, it enables designs not possible through other means. And new materials and technologies continue improving 3D print quality and capabilities.
How Does Vacuum Casting Work?
Vacuum casting is a manufacturing process for low volume production of plastic parts, typically 25-5000 units. It involves these basic steps:
A master pattern is 3D printed or machined based on the desired finished part design.
The master is placed in a two-part silicone rubber mold and liquid silicone is poured around it under vacuum.
Once cured and removed, the flexible mold has one or more cavities matching the master pattern.
Liquid urethane resin is poured into the silicone mold which is placed under vacuum to remove bubbles.
After curing, the plastic parts are removed from the mold for any finishing work before use.
The silicone mold can produce multiple castings before wearing out depending on material used.
Like injection molding, vacuum casting produces durable plastic components, but has advantages at lower volumes and for rapid prototyping needs.
Benefits and Limitations of Vacuum Casting
Below are some key benefits and limitations to consider if vacuum casting is suitable for your application:
Benefits
Relatively low cost for short run production
Fast turnaround on prototype parts
Good for complex geometries
Range of urethane material options
No need for expensive hard tooling
Limitations
Limited production run sizes
Slower than high volume injection molding
Lower dimensional accuracy than machining
Restricted size based on vacuum chamber
Production costs higher per part than injection molding
Vacuum casting bridges the gap between rapid prototyping and full-scale manufacturing. For medium production runs, it offers an affordable solution.
When to Use 3D Printing vs. Vacuum Casting
Determining whether to use 3D printing or vacuum casting depends on factors like desired material, complexity, accuracy, quantity, and budget:
3D printing is ideal for one-off prototypes, custom products, or small batches. Vacuum casting is better for runs of 25-5000 units.
3D printing can produce highly complex, enclosed geometries. Vacuum casting can handle moderately complex shapes.
Vacuum cast parts have higher dimensional accuracy and smoother finishes than most 3D printing.
A wider range of plastic materials with better mechanical properties can be vacuum cast. 3D printing materials are more limited.
3D printing has lower startup costs, but vacuum casting is more economical at production volumes.
Lead times for vacuum casting masters and molds are longer than just 3D printing parts directly.
Understanding the unique advantages of each process helps determine which is the right rapid prototyping and manufacturing solution for a given application.
Conclusion
Both 3D printing and vacuum casting provide innovative alternatives to conventional product manufacturing. 3D printing enables unprecedented geometric complexity for prototyping one-off designs. Vacuum casting is ideal for short run production before investing in hard tooling. By leveraging the strengths of each process at the appropriate stage of product development, companies can accelerate innovation and time-to-market.
Appreciate the creator